Induktives Schmieden
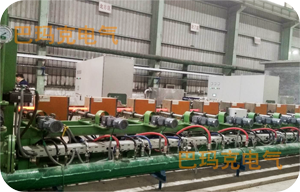
Die induktive Erwärmung für die Warmverformung bietet einen hohen Wirkungsgrad, genaue Temperaturführung, geringe Oxidation der Werkstückoberfläche und bestmöglichen Erhalt der Werkstückeigenschaften.
Da das automatisierte induktive Schmieden im Allgemeinen erfordert, bei hohen Ausgangsleistungen kontinuierlich zu arbeiten, sind der hohe Wirkungsgrad, die Zuverlässigkeit, die Lebensdauer und die Wartungskosten bestimmende Faktoren.
Der Bamac Induktionsgenerator ist ein hocheffizientes und energiesparendes Produkt, der Wirkungsgrad des Schmiedeinduktors ist höher als 96%. Der Leistungsfaktor beträgt nicht weniger als 0,9, was besonders das Stromnetz entlastet. Mit einer Lebensdauer von mehr als 15 Jahren, hoher Zuverlässigkeit und niedrigen Wartungskosten ist er ein idealer Induktionswärmegenerator für das automatisierte Schmieden.
Das induktive Schmieden ist geeignet für alle metallischen Werkstoffe wie Stahl, Edelstahl, Messing, Aluminium und Kupfer.
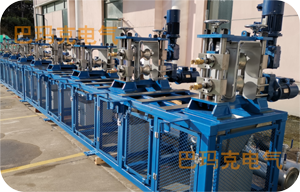
Auf der Suche nach qualitativ hochwertigen Produkten und unter dem Druck von steigenden Lohnkosten bietet sich der Einsatz von induktiver Schmiedetechnik zur Vollautomatisierung der Produktion an, um die Lohnstückkosten durch gesteigerten Durchsatz bei gesteigerter Qualität zu reduzieren. Das erfordert, dass der Induktionsgenerator über eine hochwertige automatische Temperaturregelung und eine von der SPS oder dem Steuerungscomputer zur Verfügung gestellte Schnittstelle zur Einbindung in die Fertigungslinie verfügt, welche den Ausgangszustand, den Verlauf, den Endzustand des Werkstücks und den Takt der Fertigungslinie erfassen kann. Mit der Bamac V500 Produktfamilie wurden für diese Probleme geeignete Lösungen gefunden.
Analyse der Energieeinsparung durch induktives Schmieden:
Im Vergleich mit der Erwärmung durch Öl- oder Gasbrenner, welche eine passive Erwärmung verursachen, ist die Induktion eine aktive Erwärmung. Offensichtlich ist die Effizienz der passiven Erwärmung viel schlechter. In Zahlen dargestellt, Erwärmung durch Flammen verursachen mehr als den dreifachen Energieverbrauch. Da die Kosten für elektrische Energie höher sind als für Öl oder Gas, bleibt eine Kostenersparnis von ca. 50% zugunsten der induktiven Lösung. Alleine hierdurch rentiert sich eine Investition innerhalb von 6 – 12 Monaten.
Als Nebeneffekt reduziert sich die Wärme- und Lärmbelastung der Arbeiter erheblich, was zu erhöhter Produktivität und geringerem Krankheitsrisiko beiträgt.
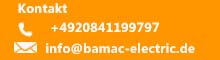